Lean Manufacturing
- Nam H Le
- Aug 21, 2024
- 4 min read
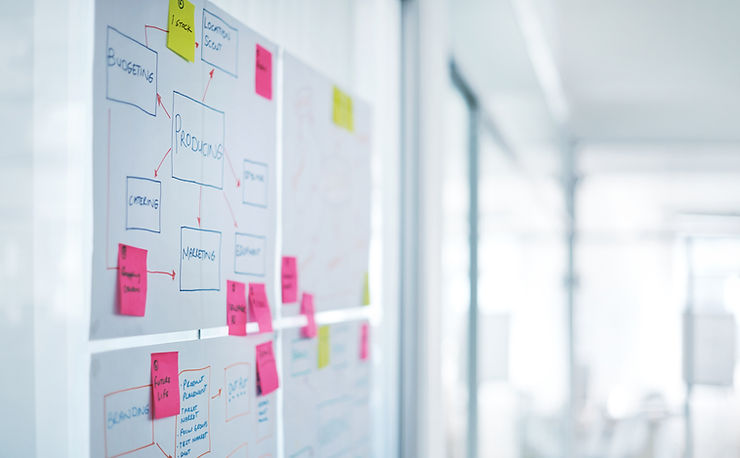
Lean Manufacturing Methodology: Revolutionizing Production Efficiency
Lean manufacturing methodology is a systematic approach to eliminating waste and maximizing efficiency in production processes. Originating from the Toyota Production System (TPS) in the mid-20th century, lean manufacturing has since become a cornerstone of modern industrial practices, helping companies across various sectors improve quality, reduce costs, and enhance customer satisfaction.
The Origins and Evolution of Lean Manufacturing
The roots of lean manufacturing can be traced back to the Toyota Motor Corporation in Japan. In the 1950s, Taiichi Ohno and Eiji Toyoda developed the Toyota Production System, which laid the foundation for what would later be known as lean manufacturing. The system was designed to improve efficiency, reduce waste, and optimize production processes in response to Japan's post-war economic challenges. As Toyota's success grew, Western manufacturers began to take notice. In the 1980s, researchers from the Massachusetts Institute of Technology (MIT) studied Toyota's methods and coined the term "lean production" to describe the company's approach. The publication of "The Machine That Changed the World" by James Womack, Daniel Jones, and Daniel Roos in 1990 further popularized lean principles in the Western business world.
Core Principles of Lean Manufacturing
Lean manufacturing is built on five fundamental principles:
Define Value: Identify what creates value from the customer's perspective.
Map the Value Stream: Visualize all steps in the production process and eliminate non-value-adding activities.
Create Flow: Ensure smooth progression of value-creating steps.
Establish Pull: Produce only what is needed when it is needed.
Pursue Perfection: Continuously improve processes to eliminate waste and enhance value
.
These principles form the foundation of lean thinking and guide organizations in their pursuit of operational excellence.
Key Concepts and Tools in Lean Manufacturing
Just-in-Time (JIT) Production
JIT is a core component of lean manufacturing, focusing on producing goods only when they are needed. This approach minimizes inventory costs and reduces waste associated with overproduction.
Kaizen (Continuous Improvement)
Kaizen is the Japanese concept of continuous improvement. It encourages all employees to constantly seek ways to enhance processes and eliminate waste.
Value Stream Mapping
This visual tool helps identify all the steps in a production process, highlighting areas of waste and opportunities for improvement.
5S Workplace Organization
The 5S methodology (Sort, Set in Order, Shine, Standardize, Sustain) is used to create and maintain an organized, clean, and efficient workplace.
Kanban
Kanban is a visual scheduling system that helps manage workflow and inventory levels, supporting the pull-based production system.
Poka-Yoke (Error-Proofing)
This technique involves designing processes and products to prevent errors and defects from occurring in the first place.
Implementing Lean Manufacturing
Successfully implementing lean manufacturing requires a systematic approach:
Assess Current State: Evaluate existing processes and identify areas for improvement.
Educate and Train: Provide comprehensive training on lean principles and tools to all employees.
Start Small: Begin with pilot projects to demonstrate the benefits of lean practices.
Map Value Streams: Visualize current processes and identify waste.
Implement Pull Systems: Transition from push to pull production methods.
Standardize Work: Develop and document best practices for each process.
Continuous Improvement: Encourage ongoing efforts to refine and optimize processes
.
Benefits of Lean Manufacturing
Organizations that successfully implement lean manufacturing can expect numerous benefits:
Reduced Waste: Elimination of non-value-adding activities leads to significant cost savings.
Improved Quality: Standardized processes and error-proofing techniques result in fewer defects.
Increased Efficiency: Streamlined processes and optimized workflows enhance productivity.
Shorter Lead Times: JIT production and efficient processes reduce time-to-market.
Enhanced Customer Satisfaction: Improved quality and faster delivery times lead to happier customers.
Greater Employee Engagement: Involving employees in continuous improvement fosters a sense of ownership and pride in their work
.
Challenges in Implementing Lean Manufacturing
While the benefits of lean manufacturing are substantial, organizations may face challenges during implementation:
Resistance to Change: Employees may be hesitant to adopt new practices and mindsets.
Short-Term Focus: Pressure for immediate results can hinder long-term improvement efforts.
Lack of Leadership Support: Without strong leadership commitment, lean initiatives may falter.
Misunderstanding of Lean Principles: Focusing solely on tools without embracing the underlying philosophy can lead to suboptimal results.
Difficulty in Sustaining Improvements: Maintaining momentum and preventing backsliding requires ongoing effort and dedication
.
Lean Manufacturing in the Digital Age
As technology continues to evolve, lean manufacturing is adapting to incorporate digital tools and concepts:
Industry 4.0: Integration of smart technologies and data analytics enhances lean practices.
Internet of Things (IoT): Connected devices provide real-time data for more accurate decision-making.
Artificial Intelligence and Machine Learning: Advanced algorithms optimize processes and predict maintenance needs.
Digital Twins: Virtual representations of physical processes enable simulation and optimization
.
Conclusion
Lean manufacturing methodology has proven to be a powerful approach for organizations seeking to improve their operational efficiency and competitiveness. By focusing on eliminating waste, creating value, and fostering a culture of continuous improvement, lean principles help companies adapt to changing market demands and customer expectations. As businesses continue to face challenges in an increasingly complex and competitive global marketplace, the principles of lean manufacturing remain as relevant as ever. By embracing lean thinking and adapting it to the digital age, organizations can position themselves for long-term success and sustainable growth. Implementing lean manufacturing is not a one-time effort but a journey of continuous improvement. It requires commitment, patience, and a willingness to challenge established practices.
However, for those organizations that successfully embrace lean principles, the rewards in terms of improved efficiency, quality, and customer satisfaction make it a worthwhile investment. As we move forward, the integration of lean manufacturing with emerging technologies and data-driven decision-making will likely lead to even greater opportunities for optimization and innovation in production processes. By staying true to the core principles of lean while embracing new tools and techniques, manufacturers can continue to drive efficiency and excellence in their operations for years to come.
Comments