Quality Management System
- Nam H Le
- Aug 21, 2024
- 4 min read
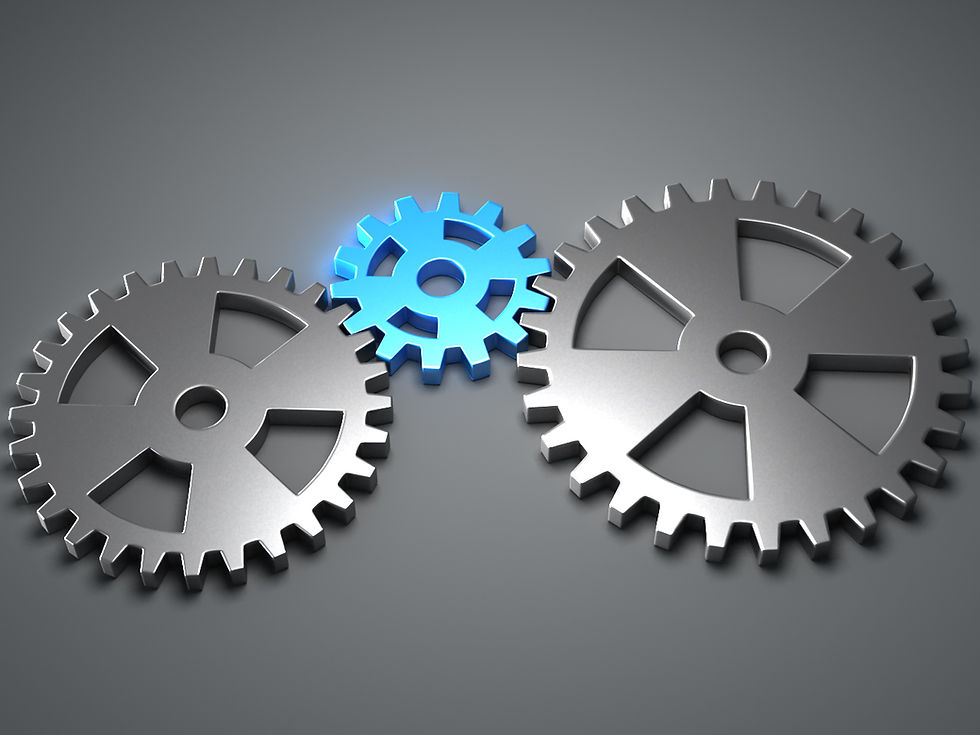
Quality Management Systems: Driving Excellence in Business Operations A Quality Management System (QMS) is a formalized framework that documents processes, procedures, and responsibilities for achieving quality policies and objectives. It serves as a cornerstone for organizations aiming to consistently meet customer expectations, comply with regulations, and drive continuous improvement. In today's competitive business landscape, implementing an effective QMS is crucial for sustainable success and growth.
Understanding Quality Management Systems
At its core, a QMS is designed to coordinate and direct an organization's activities to meet customer and regulatory requirements while improving its effectiveness and efficiency. The most widely recognized standard for QMS is ISO 9001:2015, which provides a set of criteria that organizations can use to create and maintain their quality management systems.
Key Components of a QMS
Quality Policy and Objectives: A clear statement of an organization's intentions and direction related to quality.
Quality Manual: A document specifying the QMS of an organization.
Organizational Structure and Responsibilities: Clearly defined roles and responsibilities for quality management.
Data Management: Processes for collecting, analyzing, and using data to drive improvements.
Processes: Identified and managed processes to ensure consistent quality.
Resources: Adequate resources allocated to implement and maintain the QMS.
Customer Satisfaction: Methods to measure and improve customer satisfaction.
Benefits of Implementing a Quality Management System
Organizations that successfully implement a QMS can expect numerous benefits:
Enhanced Customer Satisfaction: By consistently meeting customer requirements, organizations can improve customer satisfaction and loyalty.
Improved Operational Efficiency: Standardized processes reduce errors and waste, leading to increased productivity.
Better Decision Making: Data-driven approaches facilitate informed decision-making at all levels of the organization.
Regulatory Compliance: A well-designed QMS helps ensure compliance with relevant regulations and standards.
Continuous Improvement: Built-in mechanisms for monitoring, measuring, and improving processes drive ongoing enhancements.
Increased Employee Engagement: Clear roles and responsibilities, along with a focus on quality, can boost employee morale and engagement.
Competitive Advantage: Improved quality and efficiency can lead to a stronger market position and increased competitiveness.
Implementing a Quality Management System
The implementation of a QMS typically follows these steps:
Gap Analysis: Assess current processes against QMS requirements to identify areas for improvement.
Planning: Develop a comprehensive plan for QMS implementation, including timelines and resource allocation.
Documentation: Create necessary documentation, including the quality manual, procedures, and work instructions.
Training: Educate employees on the QMS principles, processes, and their roles in maintaining quality.
Implementation: Roll out the QMS across the organization, ensuring all processes align with the new system.
Internal Audit: Conduct regular internal audits to ensure the QMS is functioning as intended.
Management Review: Regularly review the QMS at the highest levels of the organization to ensure its continued effectiveness and alignment with strategic goals.
Continuous Improvement: Use data and feedback to continuously refine and improve the QMS.
Challenges in QMS Implementation
While the benefits of a QMS are significant, organizations may face challenges during implementation:
Resistance to Change: Employees may resist new processes or documentation requirements.
Resource Constraints: Implementing a QMS requires time, effort, and financial resources.
Maintaining Momentum: Sustaining the initial enthusiasm and commitment can be challenging over time.
Balancing Flexibility and Standardization: Finding the right balance between standardized processes and the need for flexibility can be difficult.
Integration with Existing Systems: Aligning the QMS with existing management systems and processes can be complex.
Quality Management Systems in Different Industries
While QMS principles are universally applicable, their implementation can vary across industries:
Manufacturing
In manufacturing, QMS often focuses on product quality, process control, and supply chain management. Techniques like Statistical Process Control (SPC) and Six Sigma are commonly integrated into the QMS.
Healthcare
Healthcare organizations use QMS to ensure patient safety, improve clinical outcomes, and maintain regulatory compliance. The focus is often on standardizing care processes and reducing medical errors.
Service Industries
Service-oriented businesses implement QMS to improve customer satisfaction, standardize service delivery, and enhance operational efficiency. Customer feedback mechanisms are typically a crucial component of the QMS in these industries.
Software Development
In software development, QMS often incorporates agile methodologies and focuses on continuous integration and delivery, code quality, and user experience.
The Future of Quality Management Systems
As technology continues to evolve, QMS is also adapting to new challenges and opportunities:
Digital Transformation: The integration of digital technologies is making QMS more data-driven and responsive.
Artificial Intelligence and Machine Learning: These technologies are being used to predict quality issues and automate quality control processes.
Integration with Other Management Systems: There's a growing trend towards integrating QMS with other systems like Environmental Management Systems (EMS) and Occupational Health and Safety Management Systems (OHSMS).
Focus on Risk Management: Modern QMS are increasingly incorporating risk-based thinking to proactively address potential quality issues.
Sustainability: QMS are evolving to include sustainability considerations, aligning quality objectives with environmental and social responsibility goals.
Conclusion
A well-implemented Quality Management System is a powerful tool for organizations seeking to improve their operations, satisfy customers, and achieve sustainable growth. While implementing a QMS requires significant effort and commitment, the long-term benefits in terms of improved quality, efficiency, and customer satisfaction make it a worthwhile investment for organizations of all sizes and across all industries. As businesses continue to face increasing competition and evolving customer expectations, a robust QMS provides a framework for continuous improvement and excellence. By embracing quality management principles and adapting them to their unique needs, organizations can position themselves for success in an ever-changing business landscape.
Comments